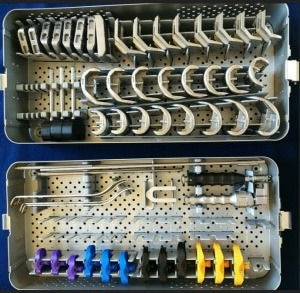
Loaners, How Did We Get Here?
John R. Harper* MBA/HCM, CRCST, CHL, CIS; David Kelman* P.E.
A universal frustration of Central Sterile Supply Departments (CSSD) across the country is that of loaner instrument sets “loaned” to hospitals and ASCs to perform surgeries of surgeon preference items. The timing of the arrival of the loaner instruments seem to never occur on the planned 24 to 72 hours prior to the planned surgery, so that they can be properly placed into the queue. Typically, these items show up later than expected, which results in a detrimental impact on the planning for the CSSD. Why is this and how did we get here?
Prior to the early to mid-1980’s hospitals purchased instrument sets and implant inventory from the major orthopaedic manufacturers. This was in the early years of total joint replacement and the technology was changing quickly. It was not uncommon to have an orthopaedic system to become obsolete in just a few years. Today it is not uncommon for a total joint replacement system to have a commercial life cycle of 15 to 20 years. While this timeline seems great, technological advancements continued to advance as does the instrumentation to deliver care. What happened was that the hospitals were left holding obsolete and expensive instrumentation and implant inventories. To avoid this from continuing to proliferate led to the evolution of the loaner instruments and implant inventory methods of today, in which the instruments and inventory remain owned by the medical device companies, and only the implants utilized during surgery are invoiced.
What also occurred during this time was the expansion and complexity of the implant systems. For example, a total knee system of 1985 could consist of only five sizes and one style of tibial bearing inserts. Today, a total knee may have ten plus sizes, sometimes in two different widths, and two to three different tibial bearing insert sizes in numerous thicknesses. Since the mid-1980’s the number of total joint replacement has increased significantly, that in 2014 there were more than 1 million procedures performed. The growth of total joint replacements is anticipated to continue to increase significantly1.
For the medical device companies, the cost of a complete set of instruments is extremely expensive. We have seen the costs of a single set of instruments range in cost from $25,000 to more than $70,000. This does not include the cost of the sterile implant inventory that has to accompany it for each surgical case. Even for large medical device companies they must carry significant amounts of instrument sets and implant inventories, that in many cases represents billions of dollars.
The medical device companies attempt to get the maximum number of “turns” that a set of instruments are utilized per month for each surgery. As significant capital and expense costs are associated with adding more loaner instrument sets and implant inventory. Thus, controlling and/or limiting the manufactures desire to increase the number of instruments sets in the field, as this has a direct impact on the financial well being of the company. Furthermore, this limited number of instrument sets must be moved around to accommodate the needed procedures, and this many times means that the loaner sets do not show up in a timely manner to the facilities in need of them. The medical device companies have centralized loaner instrument warehouse centers, that ship the instrument sets and implant inventory around the country to support the local surgical demand. Again, to minimize the requirement for creating more instrument sets.
In the CSSD the pressure continues to rise, for every implant there is an associated amount of additional instrumentation. Even if the number of surgeries remained constant, which it has not, the shear volume of instruments that the CSSD had to process increased significantly, and this is just one example. Add to this the timing as mentioned in the forefront of this article, which in early days viewed the solution as “Flash” sterilization2, which meant these items were delivered directly to the OR, and then placed in a 20-minute gravity steam sterilization cycle with no dry time and delivered directly to the operating room for use. As time progressed the term was advanced to Immediate Use Steam Sterilization (IUSS), and also had new dynamic cycles put into place which introduced a 4-minute IUSS cycle, which still accounted for a cycle with no dry time as with a conventional cycle. As with all advancements and learning, infection prevention was able to correlate a reduction in surgical site infections (SSI) by limiting the use and the number of IUSS cycles. The requirement to minimized and preferable eliminate the use of IUSS, but if used accreditation agencies required documentation stating why the use of IUSS and its necessity.3 This too has led many facilities to evoke a “Life or Limb” document where the OR team and surgeon had to sign off that the items put through an IUSS cycle was needed to save the life or limb of the patient. This added to the burden of the CSSD, having to manage these sets (decontamination, sterilization, and delivery). Processing the loaner instrument sets in the proper why significantly reduced the number of “turns” that the medical device companies could obtain, due to the timing requirements. An additional aggravation to the growing shortage of loaner instrument sets.
Do not expect this situation to improve anytime soon, in fact it will probably get more frustrating. The reasons are that as more complex surgeries are being approved to be performed in the ASC settings, which means that for medical device companies, previously had to service about 6000 hospitals, now must consider more than 5700 Medicare approved ASCs in the United States, for a possible 12,000 locations which may also require their services. In addition, the constant pressure on the medical device companies to reduce their implant pricing will also keep in check their ability to add additional loaner instrument sets.
For this to change a solution that is a win/win for the hospitals, ASCs and the medical device companies is necessary. For the medical device companies that is a means to increase the number of turns of instrument set can be utilized monthly. This will have the effect of increasing the number of available instrument sets in the field without having to build significant numbers of expensive instrument sets. But to achieve this end, the CSSD’s need additional capacity to minimize the queuing time and improve the return time for the loaner sets of instruments. This type of capacity increase by one or even two facilities in an area would have limited or no impact to this problem. An alternate solution would be a localized sterilization service center that can provide the added capacity and deliver the clean and sterile loaner instrument sets to the hospitals and ASCs. But until then the problem of availability of the loaner instrumentation sets and the impact to the Central Sterile Supply Department, is not going away anytime soon.
References
コメント